Для
многих дефектов, включая большинство дефектов внешнего вида, механизмы их
формирования остаются недостаточно изученными. Трудности изучения механизмов
обусловлены сложностью поведения термопластов в условиях литья под
давлением, а также высокими скоростями реологических, тепловых, структурных
и др. процессов в сочетании с высоким давлением и температурой, что
затрудняют получение достоверной информации непосредственно в ходе литья.
Взаимосвязь дефектов
Взаимосвязь дефектов является одним из факторов, которые необходимо
учитывать при оценке качества литьевого изделия и поиске способов устранения
брака.
Многие
дефекты внешнего вида сопровождаются изменениями свойств термопластичного
материала и структуры литьевого изделия, которые приводят к изменению
усадочного поведения, ухудшению
эксплуатационных характеристик и долговечности изделия.
Ограничения контроля технологического процесса
Хотя современные термопластавтоматы позволяют контролировать большое
количество технологических параметров [10-11], некоторые важнейшие
характеристики процесса литья термопластов под давлением остаются вне
области контроля.
В
промышленных условиях контроль температуры по зонам материального цилиндра
осуществляется с помощью датчиков, установленных в корпусе материального
цилиндра вблизи его внутренней поверхности. Температура расплава на стадии
пластикации в канале шнека и дозе расплава, набираемой в передней части
шнека, зависит от свойств полимерного материала, конструктивных особенностей
литьевой машины и других факторов.
Повышенная
неоднородность распределения температуры расплава в дозе впрыска является
следствием процесса периодической шнековой пластикации, и может быть снижена
в определенных пределах за счет ступенчатого регулирования частоты вращения
шнека, противодавления, а также использования различных профилей задания
температуры по зонам материального цилиндра [10, 12].
Тепловой
баланс полимерного материала на стадии пластикации складывается из внешних и
внутренних источников тепла, а также потерь тепла системой. К внешним
источникам тепла относятся нагреватели материального цилиндра и сопла, к
внутренним - диссипативное тепловыделение в расплаве при его сдвиговом
течении в канале шнека, а также при сжатии расплава под действием давления в
материальном цилиндре (соответственно при расширении расплава в результате
снятия давления происходит его охлаждение). Потери тепла происходят путем
теплопереноса от сопла к литьевой форме, а также через воздух (путем
радиации и конвекции). Для кристаллизующихся материалов в тепловом
балансе необходимо также учитывать количество теплоты, необходимое для
плавления полимерного материала. Тепловой баланс полимерного материала в
материальном цилиндре и соответственно температура расплава зависят от
конструкции шнека [13].
Температура расплава в материальном цилиндре может быть значительно выше
заданной температуры по зонам материального цилиндра. Например, в работе
[14] разница максимальной температуры
расплава для ударопрочного полистирола (при высокой частоте вращения шнека и
высоком противодавлении) и температуры, заданной по зонам материального
цилиндра, достигала 44
оС.
В работе [15] был замерен тепловой поток между материальным цилиндром и
полимерным материалом при пластикации полипропилена с использованием
высокочувствительных датчиков теплового потока. В области средних значений
частот вращения шнека происходил теплоперенос от материального цилиндра к
полимерному материалу, тогда как при очень малых и высоких частотах вращения
шнека наблюдался обратный тепловой поток от полимерного материала к
материальному цилиндру, что обусловлено влиянием диссипативного
тепловыделения при сдвиговом течении расплава в каналах шнека.
Высокий уровень диссипации тепла и, соответственно повышение температуры
расплава относительно температуры материального цилиндра при очень малых
частотах вращения шнека связаны с влиянием высокой вязкости расплава, тогда
как при высоких частотах вращения шнека – высокой скорости сдвига.
Детальное
экспериментальное изучение температуры расплава полипропилена в передней
части материального цилиндра литьевой машины при впрыске в открытую форму
было проведено в работе [16] с использованием проволочных датчиков,
образующих сетку. Измеренные в этой работе перепады температуры расплава по
сечению передней части материального цилиндра, а также в зависимости от
времени достигают 7
оС.
При экспериментальном изучении температуры расплава ненаполненного
полипропилена, и полипропилена, наполненного стекловолокном,
выполненном в работе [17], наблюдались более высокие перепады
температуры расплава как по сечению материального цилиндра, так и от времени
(до 22 оС), что объясняется большей скоростью впрыска.
Скачок
температуры расплава в передней части материального цилиндра, а также на
выходе из сопла литьевой машины наблюдался
во многих работах для различных типов полимерных материалов как при
литье в закрытую форму, так и при впрыске «в воздух». При литье в закрытую
форму этот скачок намного больше, чем при впрыске в воздух. Факторы,
влияющие на это явление при впрыске в закрытую форму, были изучены в работе
[18] при литье поликарбоната. Результаты этой работы свидетельствуют, что
основным фактором, влияющим на скачок температуры расплава в процессе
впрыска, являлась диссипация, вызванная
адиабатическим сжатием расплава: повышение температуры расплава при этом
происходит пропорционально увеличению давления.
В
работе [14] наблюдалось почти синхронное изменение
во времени температуры расплава ударопрочного полистирола и давления,
измеренных в литьевом цикле в передней части материального цилиндра, что
также можно объяснить влиянием адиабатического сжатия.
Таким
образом, на температуру расплава в дозе впрыска материального цилиндра
оказывает влияние конструкция отливаемой детали и литьевой формы, поскольку
адиабатическое сжатие зависит от давления (оно увеличивается в ходе стадии
впрыска), а давление и температура расплава в дозе впрыска, в частности,
повышаются при увеличении длины затекания в форме и уменьшении толщины
стенки детали.
Распространенный
метод измерения температуры расплава при впрыске с открытой формой не дает
информацию о температуре расплава в реальном процессе, т.к. при открытой
форме давление в дозе впрыска не увеличивается в процессе впрыска, и фактор
адиабатического сжатия не влияет на температуру расплава.
Таким образом, современная литьевая машина в типовой комплексации, не
содержит средств контроля фактических значений температуры расплава.
Ограниченность информации о полимерном сырье
Ограниченность информации, предоставляемой изготовителями полимерного сырья,
которое используется в промышленном производстве литьевых изделий из
термопластов, связана как с экономическими факторами (желанием изготовителей
снизить затраты на контроль продукции и др.), условиями конкуренции и
другими обстоятельствами.
Для
оценки реологических свойств литьевых термопластов на практике широко
применяется показатель текучести расплава (ПТР), который в общем случае не
характеризует текучесть в условиях литья под давлением из-за разных условий
нагружения расплава при испытаниях и в реальном процессе, влияния
вязкоупругости и др. В частности, ПТР
определяется расходом при постоянной нагрузке, тогда как процесс заполнения
формы проходит в два этапа: с постоянным расходом (скоростью впрыска) при
повышении нагрузки (давления) - на первом этапе, и постоянной нагрузке
(давлении) при уменьшении расхода – на втором. По этой причине материалы,
имеющие одинаковые ПТР, могут иметь различную длину затекания в условиях
литья под давлением.
Кроме
того, потери давления при
течении в конвергентных каналах (с уменьшающися поперечным сечением) и длина
затекания в условиях литья под давлением зависит от вязкоупругих свойств
(эластичности) полимерного расплава, тогда как ПТР характеризует текучесть
(с вышеупомянутыми ограничениями) в условиях сдвигового течения.
Существующие методы измерения вязкоупругих свойств расплава (например,
продольной вязкости) в условиях элонгационного течения редко используются
изготовителями промышленных термопластов.
В
производственной практике широко распространено добавление (до 20-30% по
весу) к сырью вторичного материала (обычно в виде дробленки), который может
содержать смесь термопластов, подвергшихся однократной и многократной
переработке. Добавление вторичного материала может оказывать влияние на
процесс литья и качество получаемых изделий, для предупреждения проблем
необходимо уделять особое внимание происхождению вторичного материала и
всему технологическому процессу его хранения и переработки. Например,
присутствие в дробленке пылевой фракции может приводить к значительному
изменению условий стадии пластикации, и негативно повлиять на качество
литьевых изделий: быстрое плавление пылевой фракции создает условия для
скольжения (последнее снижает диссипацию тепла), и формирования застойных
зон.
Влияние особенностей материала
Возникновение тех или иных дефектов и внешний вид изделий с дефектами в
большой степени зависит от особенностей марки полимерного материала:
базового полимера или смеси полимеров, а также наполнителей и добавок.
Ненаполненные термопласты можно разделить на несколько групп, для которых
характерно различное поведению в процессе литья под давлением:
- Аморфные однофазные (ПС, ПК, ПММА);
-
Аморфные двухфазные (УПС, АБС);
- Аморфные – с малой степенью кристалличности (ПВХ);
- Быстро
кристаллизующиеся (ПЭ, ПП, ПА 6, ПА 66, ПБТ);
-
Медленно кристаллизующиеся (ПЭТ, ПФС);
- Смеси
полимеров - совместимые;
- Смеси
полимеров - несовместимые (ударопрочные марки и др.);
-
Термопластичные эластомеры, эластичные термопласты (пластифицированный ПВХ).
Присутствие наполнителей может принципиально изменить свойства и поведение
термопластов по сравнению с ненаполненными системами. Значительно
различаются по поведению в условиях литья под давлением термопласты.
содержащие следующие группы наполнителей:
- Дисперсные наполнители (тальк, слюда, стеклянные шарики и др.);
-
Коротковолоконные на основе жесткого волокна (стеклянного, углеродного);
-
Длинноволоконные на основе жесткого волокна (стеклянного, углеродного).
Сложность реологического поведения полимерного материала в условиях
литья под давлением
Сложность реологического поведения расплавов термопластов при литье под
давлением обусловлена, во-первых, сложностью самой реологической среды и,
во-вторых, многообразием условий ее деформирования в процессе переработки.
Расплавы
промышленно-выпускаемых ненаполненных термопластов представляют собой
многокомпонентные системы. Основной компонент – полимер – может иметь
различное молекулярно-массовое распределение (ММР) как по ширине
(узкое или широкое), так и по форме (одномодальное, бимодальное или
мультимодальное).
В расплавах промышленных блок- и привитых сополимеров, таких как
ударопрочный полистирол, АБС и т.д., один из компонентов образует дисперсную
фазу, которая ориентируется при течении, что оказывает негативное влияние на
прочность спаев и может приводить к заметной анизотропии механических,
усадочных и других свойств материала.
Для получения необходимого комплекса технологических и эксплуатационных
свойств материала применяют различные добавки: стабилизаторы, окрашивающие
вещества, нуклеаторы, смазки и др., которые также оказывают влияние на его
реологические свойства. Кроме того, промышленные марки гранулированных
термопластов могут содержать остатки мономера, растворителя, а также
продукты частичной деструкции, протекающей в процессе получения сырья.
При переработке литьем под давлением в материал попадают продукты его
деструкции, сшивки и других процессов изменения химической структуры,
которые могут происходить в материальном цилиндре литьевой машины, а также в
форме, под действием высокой температуры, механической нагрузки, кислорода
воздуха и прочих факторов. Жидкие низкомолекулярные продукты могут
образовывать раствор с полимерным материалом или выделяться в отдельную
жидкую фазу.
Система полимер-низкомолекулярные компоненты может изменять фазовый состав
под действием повышенной температуры или течения расплава. Типичной
проблемой, например, является выделение масла, входящего в состав
композиции, при переработке мягких термопластичных эластомеров (ТПУ,
стирол-этилен-бутилен-стирольных ТЭП), которое приводит к образованию
маслянистых пятен на поверхности отлитого изделия.
Воздух, влага и низкомолекулярные легкокипящие продукты деструкции при
высоком давлении растворены в расплаве, а при давлениях, ниже критического
(давление Генри), присутствуют в расплаве в виде газовых пузырьков.
Повышенное
содержание влаги в расплаве может
возникать из-за неэффективной сушки первичного полимерного сырья,
использования невысушенной дробленки или добавок (например, пигментов,
способных поглощать большое количество влаги из-за высокой удельной
поверхности), а также концентратов на их основе [19].
Для гигроскопичных материалов
повышении влажности расплава может оказывать негативное влияние на весь
комплекс технологических и эксплуатационных свойств.
Усилия многих исследователей направлено на изучение
явлений, которое называют неустойчивым течением
[20]. В условиях литья под давлением
различают несколько видов неустойчивости [21-22].
Неустойчивое течение на входе в полость обусловлено перестройкой
фронта расплава при переходе от литниковой системы к полости. С этим видом
неустойчивости связывают матовые или мутные пятна вблизи впуска и развитие
струйного течения в полости. Другим видом является неустойчивое течение у
фронта потока, которое, как считается, вызывает дефект «тигровые полосы».
Неустойчивое течение, вызванное охлаждением фронта расплава, приводит к
дефекту «грампластинка».
Глобальные условия процесса и локальные условия в формующей полости
К глобальным условиям процесса литья (режиму литья) относятся скорость
впрыска (или профиль скорости впрыска), условия переключения на режим
управления давлением, а также профиль давления выдержки, задаваемые и
обеспечиваемые системой управления литьевой машины.
В
то же время существует большое многообразие локальных (изменяющихся от
области к области) условий для характеристик расплава в литниковой системе и
полости формы (температуры, линейной скорости течения, направления течения,
давления, объемной усадки и др.), определяемых особенностями конкретной
конструкции.
Наличие
замкнутой полости в сочетании с нестационарностью процесса, его
неизотермичностью, широким диапазоном (2-3 порядка) изменения вязкости
литьевых термопластов при изменении скорости сдвига, низкой
теплопроводностью и высокой сжимаемостью расплавов для большей части
материалов, высоким уровнем диссипации тепла при сдвиговом течении, являются
причиной значительных различий в поведении термопластов в разных зонах
отливки.
Например,
изменение локальных условий наблюдается вдоль спая, что приводит к
значительному изменению свойств отливки в разных зонах спая.
Одним из
эффективных методов изучения локальных условий при литье термопластов под
давлением является математическое
моделирование процесса (см. ниже раздел о применении компьютерного
анализа).
Структурные проблемы
Сочетание условий течения и охлаждения расплава на стадиях процесса является
причиной формирования слоевой структуры литьевых изделий из
кристаллизующихся термопластов
[23-24]. Так как свойства материала изменяются от слоя к слою
литьевое изделие можно рассматривать как слоистый композит.
Слоевая
структура образуется также при литье под давлением изделий из двухфазных
блок- и привитых сополимеров и смесей полимеров (в этом случае слои
различаются ориентацией частиц дисперсной фазы)
[25-26], а также из
термопластов, содержащих жесткий волокнистый наполнитель (с разной
ориентацией наполнителя в слоях)
[27-28].
В
литьевых изделиях из однофазных аморфных материалов распределение степени
ориентации и плотности существенно различаются по слоям
[29-30] хотя в этом случае не
принято говорить о слоевой структуре.
Инструментальные методы выявления
дефектов
Ряд экспериментальных методов выявления и изучения дефектов литьевых изделий
из термопластов получил широкое распространение в научной и производственной
практике. Среди таких методов: взвешивание деталей, оптическая микроскопия,
измерение цвета и блеска, применение измерительных калибров для отдельных
деталей, поддонов для групп деталей, измерения линейных размеров и
отклонений формы, поляризационно-оптический метод для контроля остаточных
напряжений в деталях из прозрачных или полупрозрачных материалов и др.
При
всей своей простоте взвешивание является эффективным методом контроля
процесса литья, поскольку вес изделия во многих случаях является одним из
немногих интегральных показателей качества, зависящим от свойств материала,
условий заполнения и уплотнения отливки, взаимосвязанным с качеством
поверхности изделия и его размерной точностью [31-33].
К традиционным инструментальным методам, применяемым в научных
исследованиях, относится изучение слоевой структуры микросрезов в
поляризованном свете при небольшом увеличении, хотя данный метод редко
используется в производственных условиях.
В
последние годы большое внимание уделяется применению ультразвука для
контроля процесса литья и качества изделий (например, для обнаружения утяжин
непосредственно в ходе литья [34]).
Развитие технических средств видеофиксации и анализа дефектов (тех же утяжин
[35]) на основе полученных изображений также может стать составной частью
системы контроля на производстве.
Разработка новых
эффективных и экономичных инструментальных методов контроля литьевых изделий
является актуальной задачей.
Применение компьютерного моделирования в анализе причин брака
Компьютерный анализ литья термопластов под давлением широко применяется как
для прогнозирования и предупреждения появления дефектов литьевых изделий (на
этапе подготовки производства), так и в качестве инструмента для анализа
причин брака, выявленного при испытании изготовленной формы или в процессе
производства (если, например, анализ не проводился, была произведена замена
материала, литьевой машины и т.д.) и поиске экономичных способов его
устранения.
Среди
важнейших преимуществ использования компьютерного анализа для анализа причин
брака и выборе методов его устранения:
- Возможность изучения влияния конструктивных изменений (поскольку
экспериментальные работы, связанные с конструктивными изменениями, крайне
дорогостоящие);
-
Возможность получения информации о локальном поведении полимерного материала
в литьевой полости;
-
Дополнительные возможности учета влияния особенностей материала изделия и
литьевого оборудования на процесс литья.
Так как в сеточных методах математического моделирования сетка может
оказывать очень большое влияние на точность получаемых результатов, учет
этого фактора является важнейшим условием получения корректных оценок. Также
важно учитывать особенности применяемого метода (технологии) анализа,
условия моделирования течения и охлаждения, используемые модели процесса
литья и материала, а также модели качества.
Обычно анализ причин брака с использованием компьютерного моделирования
включает следующую последовательность расчетов:
-
Анализ для фактических условий, задачей которого является воспроизведение
дефектов;
- Анализ с
оптимизацией условий, позволяющий выявить основные факторы, которые влияют
на качество изделия;
- Поиск
наиболее экономичных методов устранения брака с применением вариантного
анализа, методов планирования эксперимента.
Анализ причин брака должен базироваться на комплексном технологическом
подходе, предполагающем рассмотрение всех аспектов процесса литья, а не
только тех, которые учитываются в конкретном программном продукте. Для этого
требуется хорошая базовая подготовка специалиста, выполняющего расчеты, в
области технологии, полимерного материаловедения и др.
Анализ чувствительности по методу Тагути
Большое количество факторов, влияющих на появление дефектов при литье
термопластов под давлением, и взаимовлияние факторов может значительно
затруднить процедуру поиска приемлемого решение.
Для
выбора факторов, оказывающих наибольшее влияние на качество литьевых
изделий, в современной научной и производственной практике широко
применяется анализ чувствительности по методу Тагути. Данный вид анализа
предусмотрен также и в продуктах
Autodesk
Simulation
Moldflow
Insight.
В последние годы анализ чувствительности по методу Тагути стал одним из
наиболее распространенных методов планирования эксперимента в литье
термопластов под давлением (см., например, [36-43], что объясняется крайне
небольшим количеством экспериментов (расчетов), которые необходимо провести
для получения требуемого набора данных.
В методе Тагути на начальном этапе изучения объекта часто учитываются только
главные эффекты, и не учитывается взаимодействие факторов. В общем случае
можно учесть и взаимодействие контролируемых факторов (см., например, [43]).
К принципиальным недостаткам метода относят влияние возможной
взаимозависимости контролируемых и неконтролируемых факторов [44], что может
исказить общую картину при оценке рейтинга.
С
точки зрения традиционной методологии планирования эксперимента метод Тагути
не является строгим, однако и при использовании традиционных подходов на
практике часто пропускают важные, но длительные процедуры проверки
статистических гипотез, которые обеспечивают «строгость» всего подхода
(последнее было использовано Тагути в качестве одного из аргументов в пользу
разработанного им метода).
В
методе Тагути используется обобщенный отклик системы, называемый отношением
сигнал/шум (S/N),
под «сигналом» здесь понимаются учитываемые, под «шумом» - неучитываемые
факторы. В зависимости от особенностей изучаемого объекта применяются
следующие варианты расчета отношения сигнал/шум [45]:
- «Как
можно
большее» (Larger-the-better):
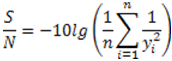
- «Как
можно
меньшее»
(Smaller-the-better):
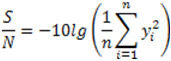
-
«Некоторое конечное»
(Nominal-the-better):
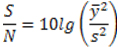
где
yi
– данные эксперимента (расчета);
n
– число экспериментов (расчетов);
– среднее значение;
s2
- стандартное отклонение, определяемое по формуле:
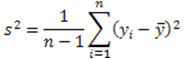
При изучении прочности изделий используют вариант «как можно большее», а при
изучении глубины утяжин - «как можно меньшее», поскольку соответственно
повышение прочности и уменьшение утяжин являются желательными событиями.
При наличии
достаточного количества измерений при экспериментальных параллельных
измерениях отношение сигнал/шум рассчитывается для
yi,
относящихся к одному эксперименту. Если измерений недостаточно, например,
при моделировании процесса, отношение сигнал/шум определяется для каждого
уровня фактора: по всем экспериментам 1-го уровня фактора
A,
по всем экспериментам 2-го уровня фактора
A,
и т.д.
Обычно в
методе Тагути применяются два или три уровня факторов, которые могут быть
непрерывными или дискретными. При использовании двух уровней для
непрерывного фактора 1-й уровень соответствует минимальному значению фактора
в условиях эксперимента (расчетов), 2-й – максимальному. Для плана с тремя
уровнями 1-й уровень соответствует минимальному значению, 2-й - среднему,
3-й - максимальному. В качестве дискретного фактора может использоваться,
например, геометрическая форма объекта.
В продуктах
Autodesk
Simulation
Moldflow
Insight
пользователь может выполнить анализ чувствительности по методу Тагути
практически для любых видов расчетов, реализованных в программном продукте,
но применяются только непрерывные факторы. Одним из факторов может быть
толщина стенки изделия.
В методе
Тагути используются ортогональные планы первого порядка (термин
«ортогональность» означает, что в каждой паре столбцов плана имеются все
комбинации уровней факторов, и все они встречаются одинаковое число раз).
Основным
результатом анализа чувствительности по методу Тагути в продуктах
Autodesk
Simulation
Moldflow
Insight
является рейтинг учитываемых факторов, который определяется выраженной в
процентах относительной величиной, рассчитываемой из соотношения сигнал/шум
(сумма рейтингов всех учитываемых факторов составляет 100%).
При
использовании метода Тагути применительно к моделированию процесса,
необходимо учитывать, в частности то, что результаты расчета рейтинга в
большой степени зависят от заданных интервалов варьирования факторов
(таблица 2). Расширение интервала варьирования, с одной стороны, приводит к
повышению рейтинга фактора, с другой - может вызывать проблемы, связанные с
применяемыми алгоритмами. Например, проблемы могут быть вызваны недоливом
[46] при расчете с низкими
значениями температуры расплава и формы, высоким значением времени впрыска,
малой толщиной стенки (при большом геометрическом масштабном коэффициенте).
Таким образом,
для получения корректных оценок в анализе чувствительности
при моделировании интервалы варьирования факторов должны быть
максимально приближены к интервалам варьирования факторов в реальном процессе.
Таблица 2. Оценка факторов, влияющие
на давление при впрыске для отливки из тальконаполненного полипропилена,
толщиной 1 мм; расчет в
Autodesk Simulation
Moldflow
Insight 2013 |